
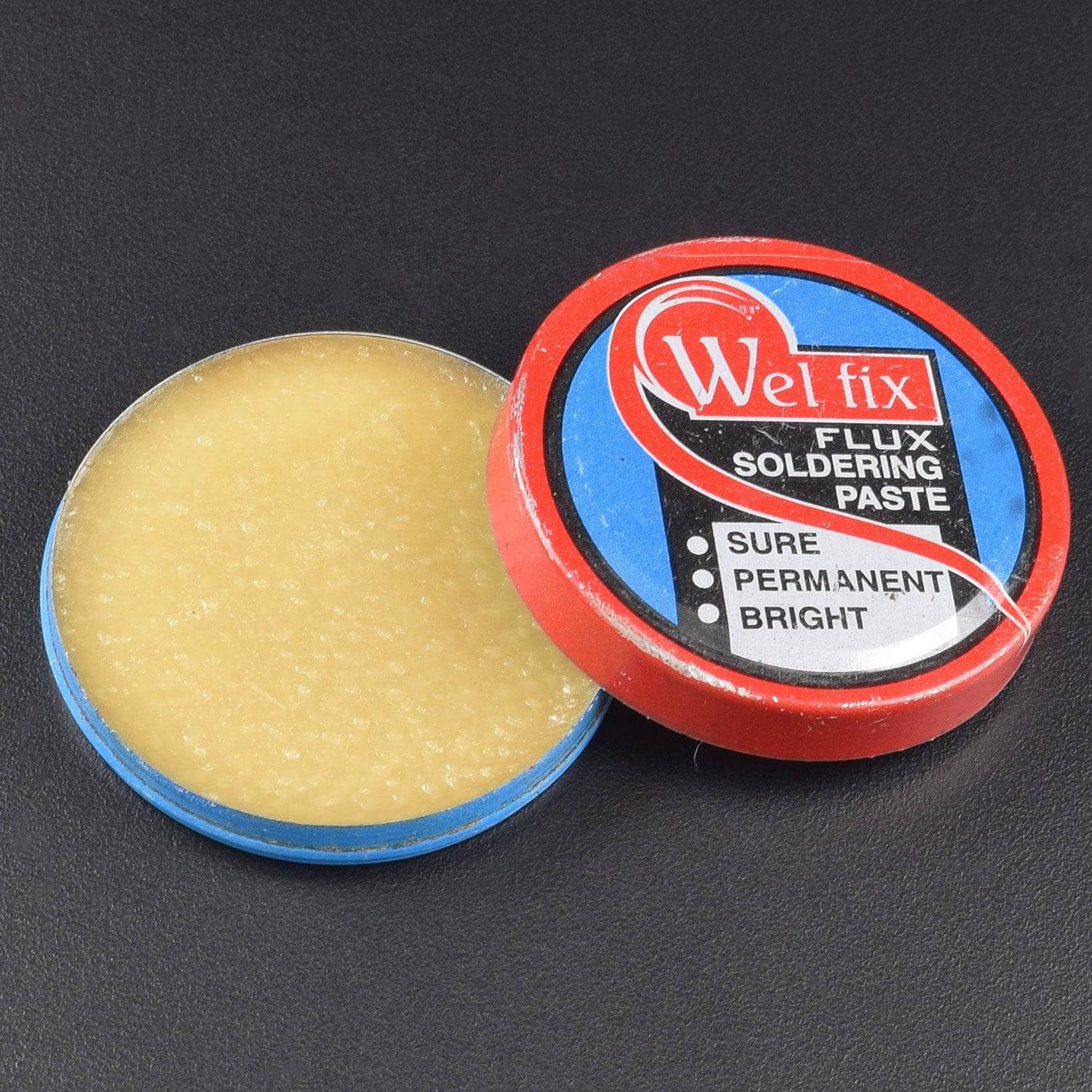
- High bond strength, PH value-neutral, insulation is strong, welding surface smooth
- IC and PCB for no corrosive
- Its boiling point only slightly higher than the melting point of the solder
- For mobile phones, PC cards, and other sophisticated electronic chip-level help welding
Description:
Soldering component is an essential element of electronics. Solder does not always bond well to components which can result in a bad solder joint, bridged pins, or even no joint at all. The solution to solder bonding issues is the use of a fluxing agent and the right temperature. When the solder melts and forms a joint between two metal surfaces, it actually forms a metallurgical bond by chemically reacting with the other metal surfaces. A good bond requires two things, a solder that is metallurgically compatible with the metals being bonded and good metal surfaces, free of oxides, dust, and grime that prevent good bonding. Grime and dust can easily be removed by cleaning or prevented with good storage techniques. Oxides, on the other hand, need another approach.
Features:
- High bond strength, PH value-neutral, insulation is strong, welding surface smooth
- IC and PCB for no corrosive
- Its boiling point only slightly higher than the melting point of the solder
- For mobile phones, PC cards, and other sophisticated electronic chip-level help welding
Types of Flux:
- Rosin Flux
Some of the oldest types of flux used are based on pine sap (refined and purified) called rosin. Rosin flux is still used today, but typically is a blend of fluxes to optimize the flux, its performance, and characteristics.
- Organic Acid Flux
One of the more common fixes used is water-soluble organic acid (OA) flux. Common weak acids are used in organic acid flux, such as citric, lactic, and stearic acid among others.
- Inorganic Acid Flux
A stronger option that organic flux is inorganic flux, which is typically a blend of stronger acids like hydrochloric acid, zinc chloride, and ammonium chloride. Inorganic acid flux is targeted more towards stronger metals such as copper, brass, and stainless steel.
Uses:
In soldering of metals, flux serves a threefold purpose: it removes oxidation from the surfaces to be soldered, it seals out air thus preventing further oxidation, and by facilitating amalgamation improves wetting characteristics of the liquid solder. Some fluxes are corrosive, so the parts have to be cleaned with a damp sponge or other absorbent material after soldering to prevent damage. Several types of flux are used in electronics.
Package Included:
1 x Soldering Tin Advanced Solder Products Electric Soldering Iron Welding Fluxes For PCB/BGA/PGA/SMD Repair Tools